An automatic heat transfer machine typically refers to equipment designed to transfer heat between two or more substances automatically, with minimal human intervention. These machines are often used in industrial processes, manufacturing, or laboratory environments where precise control of temperature and heat flow is required. Here are some common types of automatic heat transfer machines:
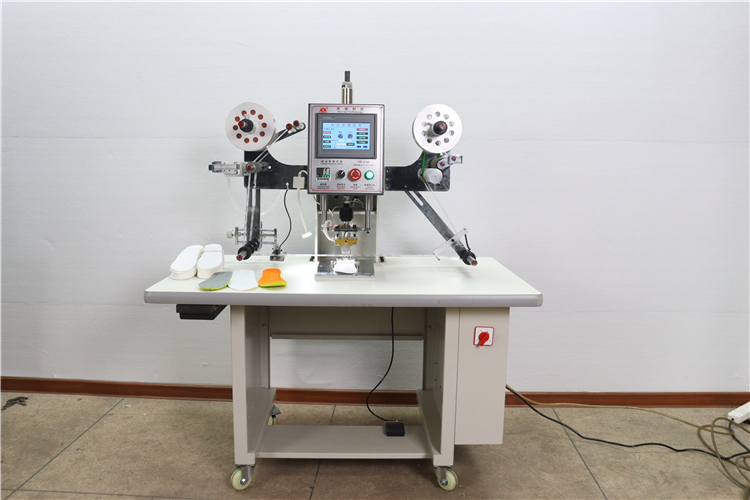
1. Heat Exchangers
▪ Purpose:
Transfer heat between two or more fluids (liquid or gas) without mixing them.
▪ Types:
Shell and Tube Heat Exchanger: Common in industries like oil refining and power plants.
Plate Heat Exchanger: Used in food processing and HVAC systems.
Air Cooled Heat Exchanger: Used where water is scarce or needs to be conserved.
Automation: These devices can be automated for continuous monitoring and adjustment of parameters like flow rate, temperature, and pressure to ensure efficient heat transfer.
2. Induction Heaters
▪ Purpose:
Use electromagnetic induction to heat a material, typically metal, through eddy currents.
▪ Automation:
Induction heaters can be automated to adjust temperature and power levels for specific heating profiles. Common in applications like metal hardening and brazing.
3. Heat Transfer Fluid (HTF) Circulators
▪ Purpose:
Circulate heat transfer fluids through systems for various applications (e.g., solar collectors, geothermal systems, and industrial cooling).
▪ Automation:
The flow rate, pressure, and temperature of the fluid can be automatically controlled based on the system's demand.
4. Hot Runner Systems
▪ Purpose:
In injection molding, these systems keep the plastic material in the mold at a specific temperature.
▪ Automation:
The temperature and heat distribution across the system can be automatically regulated to ensure uniform molding.
5. Thermal Management Systems for Electronics
▪ Purpose:
Manage the heat generated by electronic components like processors, batteries, and power electronics.
▪ Automation:
Automated cooling or heating systems (such as liquid cooling loops or heat pipes) that adjust based on thermal feedback to ensure the electronics operate within safe temperature ranges.
6. Heat Transfer for Food Processing
▪ Purpose:
Used in pasteurization, sterilization, and drying processes.
▪ Automation:
Machines in food processing plants, such as automated steam exchangers or pasteurizers, often have temperature sensors and automated control systems to ensure optimal heat treatment.
7. Automated Furnace or Kiln Systems
▪ Purpose:
Used in ceramics, glass manufacturing, and metal forging, where precise heat control is necessary.
▪ Automation:
Automatic temperature regulation and heat distribution mechanisms are integrated to achieve uniform heating.
Features of Automated Heat Transfer Machines:
▪ Temperature Sensors:
To monitor and adjust the temperature in real-time.
▪ Flow Control:
Automatic regulation of liquid or gas flow to optimize heat transfer efficiency.
▪ Feedback Systems:
To adjust the machine settings based on real-time conditions, such as pressure, flow rate, or temperature.
▪ Remote Monitoring and Control:
Many systems come with SCADA (Supervisory Control and Data Acquisition) systems or IoT (Internet of Things) capabilities for remote monitoring.
Post time: Dec-27-2024